We drive, track, and help you improve the processes
Become the Factory of the Future by making Step-by-step improvements with us. At first, we will support your Team with the Process Execution. Then, analyze the effectiveness and uncover the bottlenecks to support your continuous improvement.
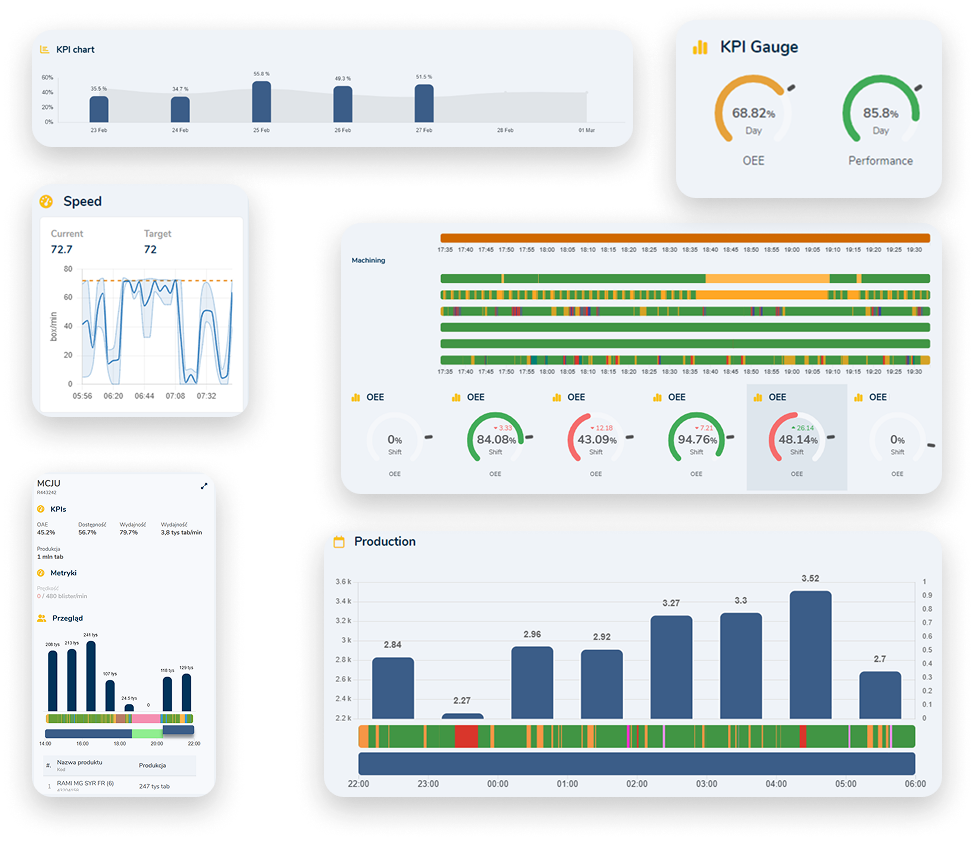
Be aware of the present situation
Surely not everyone has to know everything about every detail of the processes on production. What is important, however, is to empower the right people with the right information, to let them take care of their area.
That is why within our system, you can configure the widgets you are seeing, together with the scope of their presentation. Whatever setup, you make, your data will always be up to date.
Build Operator's Center of Execution and Improvement
We always want to support factories Agility. As your process is improving continuously or adapting to new requirements, your reports have to be updated as well.
Version Control support gives you the comfort of the smooth release of updated Report Templates without losing any previous stages.
Draft Versions support lets you iteratively work on the new Template of the Report, without distraction on Production. Once your work is finished and approved, a new version of the Report Template is activated with a single click.
Digitize Processes Reporting
Make your process data available to be used, analyzed and support your Step-by-step Improvements. Create, design, update and execute any reports, you were performing on paper, within Excel, or Word templates.
All the forms are responsive and adjusted to PC, Tablet or Smartphones, so can be used wherever you like.
Mange and track Quality Reports, Changeover steps, Planned Maintenance Activities, Deviation Reports, Center Line, and many other general, or process specific reports.
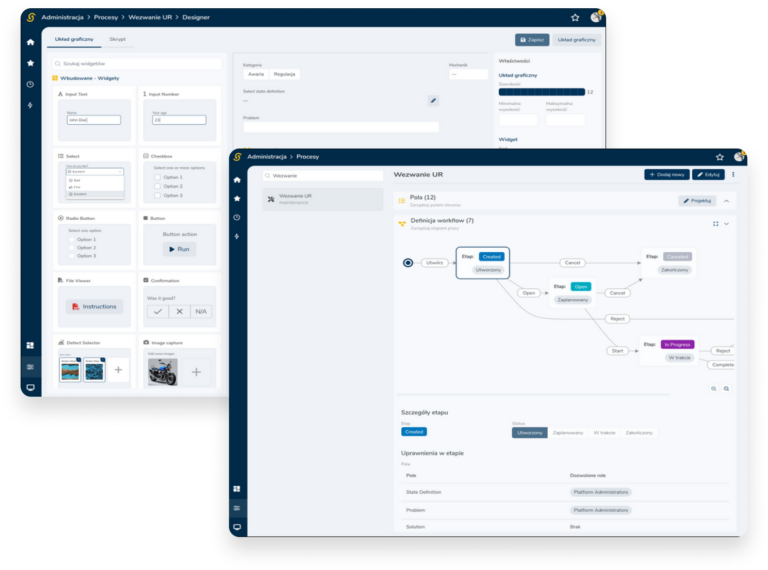
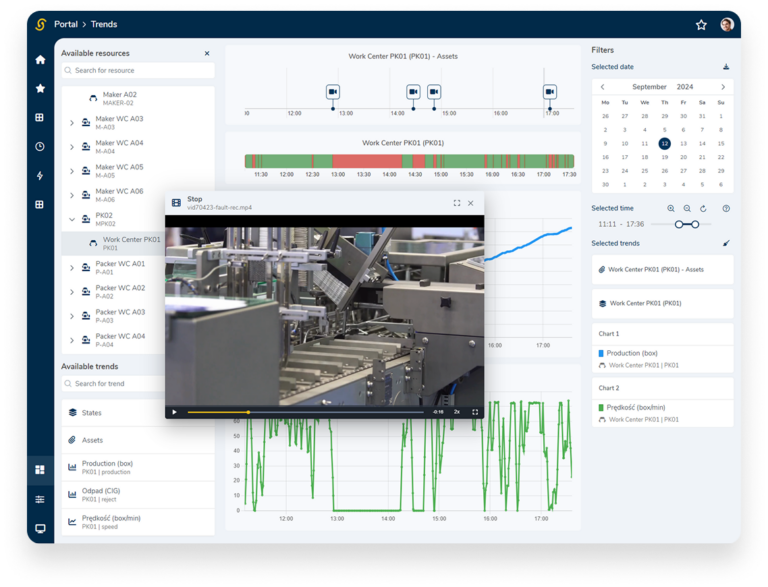
Distribute the knowledge
System is equipped with Knowledge Module to manage all the content you want to share with the teams on shop flor. With the flexible tagging system, you can always quickly find and filter the content you need at the moment.
You can also embed links to your Digital Materials on your process reports to have the right information at hand wherever you need it
Invite your team to make a change
Both Agile and Lean approaches define well-utilized knowledge and experience of employees as one of the key points of the improvement process. We fully believe in that, as we have seen many times the great results it can bring.
We are providing tools for the operators and leaders to support the creation, discussion, and application of initiatives coming from the field workers
Find your biggest losses
Work on specific stops
Planned Stops, Unplanned Stops, and Small Stops (or Micro stops) are 3 out of 6 Big Losses.
The Stops Analysis tool can be helpful during your improvement of specific stops reasons. You can work on a single work center, or group of machines (eg. the same technology)
The same as for OEE losses, analysis is done from the different perspectives, but also you can focus on different aspects of your stops like Total Duration, Number of Occurences, Avg. duration (MTTR), Avg. time between (MTBF) and others.
Features list
Intuitive Operator Portal
Wether you are running batch, or discrete processes it will be perfectly adjusted
Paperless Module
Create, manage and execute process reports on PC Tablets or Smatphones
Equipment connecton
We support most popular Industrial standards to talk with your equipment.
Real-time OEE Tracking
OEE and its components available at any time for everyone involved.
Knowledge Module
Share always up to date materials with all who needs them
Equipment Management
Define machine cycle times, expected efficiences, stop and reject reasons specific to its type.
Insightful analysis
Effectively find the source of biggest productivity losses
Statuses Management
Categorize stops and apply commenting rules (eg. for long stops)
Orders & Master Data Integration
Integrate data rather than duplicate.
Users Management
Manage users and assing roles with RBAC approach
Questions - contact us
We will be happy to answer your questions or discuss new ideas.